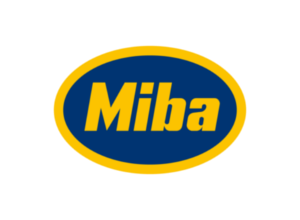
VORCHDORF. Miba Sinter Austria has carried out a BigStep® Workshop with MCG, in February 2012, to increase profitability. The new Managing Director Mr. Thomas Fenzl assesses the results in an interview with Markus Gahleitner in December 2012.
Mr. Fenzel, since February 10 months have passed. It is a good moment to talk about sustainable results. How satisfied are you personally with the execution of the projects and measures defined in our BigStep® Workshop?
Very satisfied. At the beginning of the execution process we have been concerned about the amount of the projects. All in all we are talking about 50 smaller and larger projects.
With so many projects a prioritization of the projects is recommended. What have been done at Miba Sinter Austria to ensure the execution?
After the BigStep® Workshop the project leaders have been commissioned to complete their project assignments. The next step was the definition of a steering committee. Every Wednesday the project leaders presented their progress within 15 minutes. According to the next planned milestone of the project the next presentation date has been defined together with the project leader. Through this joint definition we achieved a high commitment of the staff and renounced other ways of prioritization. Further, we used a simple project management tool based on Excel to observe the progress and current status of every single project. Based on this consequent tracking we achieved a high momentum of execution.
Thinking about the execution rate of the defined projects and measures, 10 months after the BigStep® Workshop. How many projects could be completed already?
The current execution rate is between 80% and 90%. So at a very good level.
The topic of the BigStep® Workshop was to increase the profitability (Euro). May I ask you how many Euros have been saved based on the defined projects?
About € 3 M calculated with conservative and pragmatic assumptions. The calculation of positive effects of single projects is not always unambiguously. Some things like the reduction of energy costs can be evaluated easily. Others, like machine downtimes cannot be calculated clearly, but have indirect effects on lower special transportation costs or additional contribution margins achieved through saved time. Nevertheless, our focus was the execution of the projects, not the assessment.
What is the feedback of your staff?
Extremely positive. BigStep® has become a real term at Miba, especially due to the BigStep® Info Trophy. For this, our dining room has been equipped with 8 info boards, one for every key topic. Every project was assigned to one of these key topics. On every board, information on the initial situation, current status and targets have been listed. Through a cycle of 10 – 15 minutes (8 times) more than 120 employees got informed.
What is the secret of BigStep® from your point of view?
Main focuses are defined together. Thus, a commitment within the management team is created as well as a focus on issues and targets to be worked on. This alignment within two and a half days (Workshop) is really great. Of course, there are preconditions based on the budget, which areas have to be optimized. It is almost impossible to coordinate 50 projects, beside the daily business, without any conflicts of the single targets, if every person in charge only focuses on his part. Further, the mutual understanding has been increased with the BigStep® Workshop.
Are you going to plan a BigStep® Workshop in the following year?
Yes, we need again more than 30 projects to achieve our ambitious budget targets.
Many thanks for the Interview.