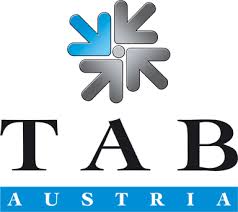
Ausgangssituation
Die Firma TAB-Austria GmbH, mit Sitz in Linz, Österreich, ein Unternehmen der Unterhaltungselektronikbranche, welches Infotainment – Terminals herstellt, vollzog eine Umstellung des Produktionssystems von einer klassischen Losgrößenfertigung auf ein JIT Fertigungssystem.
Eine erhebliche Reduktion des Lagerstandes und Umlaufvermögens war ein erster Erfolg. Die Lieferzeiten wurden dramatisch reduziert, wodurch neue Kunden gewonnen werden konnten. Aufgabenstellung für ein weiteres Six Sigma Projekt war die Erhöhung der Produktivität bei gleichzeitig weiterer Flexibilisierung um 30 – 40%.
Vorgehensweise
1. Schritt:
Hier wurde die Ist-Situation erfasst (durchlaufzeitrelevante Prozessstufen, klare Darstellung der Kundenanforderungen). Mittels Ishikawa Diagramm wurden die Haupteinflussfaktoren auf die Produktivität ermittelt.
2. Schritt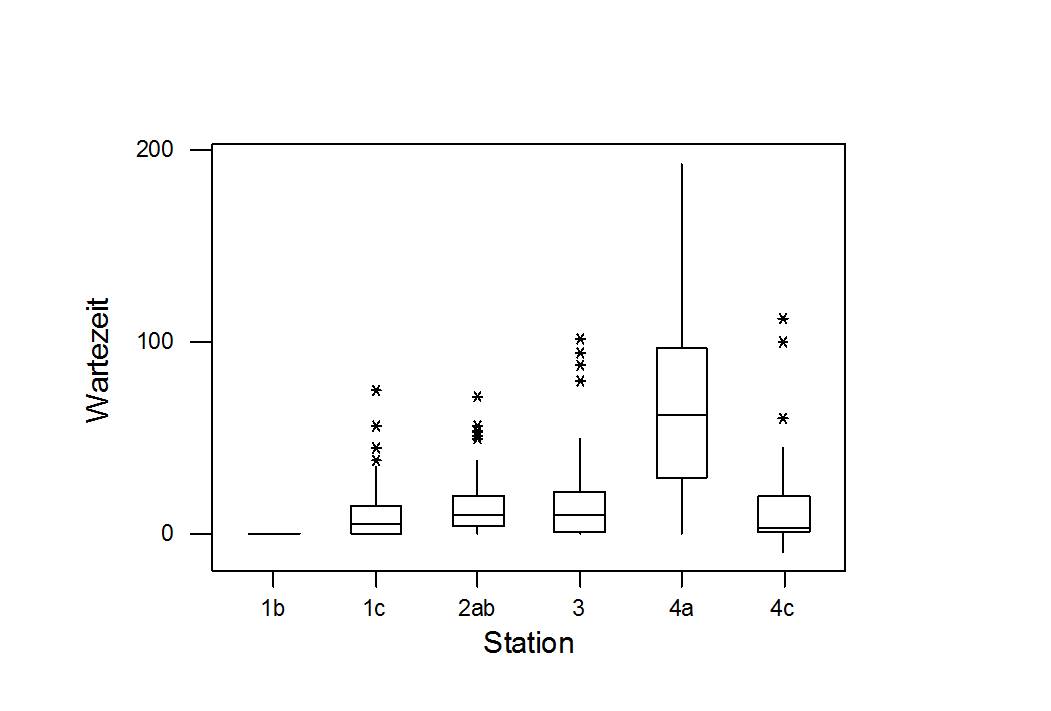
Rasch wurde ersichtlich, dass die Arbeitszeiten beim Gerät einer viel stärkeren Shwankung unterworfen war, was im Resultat eine sehr lange Wartezeit beim vorletztenProzessschritt (4a) zur Folge hatte.
3. Schritt:
Wir begannen in der Analysephase mit dem Aufstellen von Hypothesen (Zusammenfassung von Meinungen) über die zu lange Durchlaufzeit und damit den zu geringen Output und reduzierten diese anschließend in einem auf Daten und Fakten basierenden Diskussionsprozess auf 5 Störfaktoren (1. Personal wird aus Linie abgezogen, 2. Material ist nicht vorhanden, 3. ungleichmäßige Arbeitsverteilung, 4. mangelhafte Qualität der Vorarbeiten, 5. Warten auf Output der vorgelagerten Prozessstufe).
4. Schritt:
Nun war es an der Zeit, die erkannten Störgrößen zu eliminieren und versuchsweise in einem Piloten die Erfolgswirkung unserer Maßnahmen zu überprüfen.
Die Ergebnisse des Piloten waren überwältigend. Wurden im alten Prozess ~3,1 Geräte/Stunde gefertigt, konnten nun 5 Geräte/Stunde produziert werden. Die Durchlaufzeit je Gerät reduzierte sich um 80%, die Arbeitszeit um 20% und die Wartezeit zwischen den Stationen um 85%.
5. Schritt:
Um die im Piloten erzielten Ergebnisse auf Dauer sicherzustellen, wurden Process Scorecards mit den wesentlichen Prozesskennzahlen erarbeitet. Weiters wurden Regelkarten eingeführt, die die Mitarbeiter bei Überschreitung der Toleranzgrenzen veranlassen, Gegenmaßnahmen zur Beseitigung der Prozessstörung einzuleiten.
Ergebnisse
Der Output konnte um 44% gesteigert werden und die Durchlaufzeit konnte um 48% reduziert werden. Durch die Kombination der Six Sigma Verbesserungsmethodik mit den JIT-Prinzipien konnte innerhalb von 18 Monaten eine EBIT Verbesserung von 2% auf 9,5% erzielt werden.