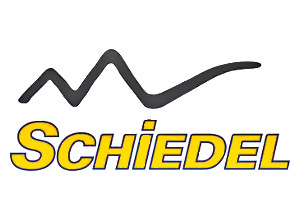
Ausgangssituation
Im Frühjahr 2008 wurde im Schiedel Werk Schöllnach mit Unterstützung durch MCG ein Just in Time Projekt begonnen, mit dem Ziel die Produktivität zu erhöhen sowie Umlaufbestände, Lagerbestände und Durchlaufzeiten zu reduzieren. Das vormals installierte Produktionssystem, eine klassische Losproduktion mit starker Fokussierung auf die Arbeitsplatz – Produktivitäten, musste aufgrund geänderter Rahmenbedingungen verändert werden. Die Notwendigkeit, die Lagerbestände stark zu reduzieren und eine 100% Lieferverfügbarkeit sicherzustellen, führten zur Entscheidung ein Just in Time Fertigungssystem einzuführen.
Vorgangsweise
Nach einer detaillierten Analyse der Ausgangssituation konnten gemeinsam mit dem Projektteam anspruchsvolle und doch erreichbare Ziele definiert und deren Erreichung über regelmäßige Projektmeetings sichergestellt werden.
In einem ersten Umsetzungsschritt wurde ausgehend vom Kundenbedarf eine notwendige Taktzeit ermittelt und dann ein Produktionslayout erarbeitet, das bei Putztüren im 30 Sekunden Takt und bei Konen im 40 Sekunden Takt die Werkstücke durch den Fertigungsprozess fließen lässt. Dies führte zu einer dramatischen Reduktion der Umlaufbestände auf nahezu Null. Durch eine Optimierung der Arbeitsweise, vor allem an den Pressen konnte zudem eine direkte Steigerung der Produktivität (gemessen als Personalminuten/Stück) erreicht werden.
In der zweiten Phase wurde verstärkt auf die Notwendigkeit der Flexibilisierung Rücksicht genommen. Dies setzt neben kurzen Durchlaufzeiten vor allem kurze Rüstzeiten voraus.
Nach einer Videoanalyse und Bewertung mit der 4 Step Rapid Setup Methode (internes/externes Rüsten/Parallelisierung/Optimierung internes Rüsten) konnte so z.B. in der Putztürfertigung ein neuer Rüstablauf definiert werden, der eine verkettete Rüstung der Pressen und des Taumlers vorsieht und damit die Stillstandszeit von mehr als einer Stunde auf rund 15 Minuten reduziert werden konnte.
Von besonderer Bedeutung im Rahmen dieses Projekts war die ständige Einbeziehung der erfahrenen Mitarbeiter. Es wurde visuelles Management und ein kontinuierlicher Verbesserungsprozess (KVP) eingeführt und versucht die Probleme und Verbesserungsideen so rasch wie möglich zu lösen bzw. umzusetzen.
Nachdem im Juli 08 die Umstellungen auf der Putztürlinie umgesetzt und weitere Verbesserungspotenziale erkannt wurden, befindet man sich in einem permanenten Verbesserungsprozess der noch längere Zeit nicht abgeschlossen ist. Vor allem durch neue/geänderte Produktvarianten (z.B. Putztürtype III) ergeben sich immer wieder neue Herausforderungen auf die mit kreativen Lösungen eingegangen werden muss.
So wurden erst im Herbst 08 Änderungen im Arbeitsablauf vorgenommen um die gesetzten Ziele zu realisieren.
Ergebnisse
Im Laufe des Jahres 2008 wurde der Lagerstand von mehr als 40.000 Stück Putztüren um ~70% auf rund 13.000 Stück Putztüren reduziert bei Erhalt einer 100%igen Lieferverfügbarkeit.
Der Umlaufbestand konnte bei den Putztüren auf nahezu Null und die Durchlaufzeit einer Putztüre auf 84 Minuten reduziert werden.
Durch die Reduktion der Handlingstufen um ~25% und Reduktion von Förderbändern und Distanzen zwischen den einzelnen Prozessstufen konnte auch eine 30%ige Platzersparnis erzielt werden.
Durch das neue Rüstkonzept mit 3 Mitarbeitern wird die Rüstzeit von vormals 1,5 Stunden auf rund 15 Minuten reduziert und damit die Flexibilität nachhaltig gesteigert.
Die Stückzeit je gefertigter Putztüre konnte von 5,6 Minuten (Basis Jan – Mai 08) auf 4,6 Minuten im März 2009 reduziert werden, was einer Produktivitätssteigerung von ~18% entspricht. Das angepeilte Produktivitätsziel von +22% wird durch die Implementierung bereits eingeleiteter Verbesserungsmaßnahmen voraussichtlich im Mai 2009 erreicht.