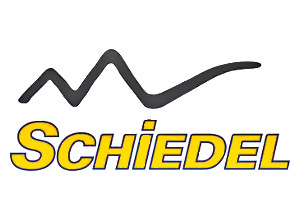
Ausgangssituation
Die Schiedel AG betreibt mehrere Produktionsstandorte in Europa, von dem einer in Italien, in der Nähe von Mailand, liegt. Von diesem Werk werden Italien, Deutschland, Österreich, Slowenien und weitere Märkte im Osten mit Stahlkaminen und –zubehör versorgt.
Um eine hohe Lieferverfügbarkeit sicherzustellen wurden hohe Lagerbestände vorgehalten, da die Flexibilität und Produktivität in den Zentralproduktionsstätten nicht ausreichend war.
Vorgangsweise/Umsetzung
- Im ersten Schritt wurde das Produktportfolio, Kundenanforderungen, Poduktanalyse, Durchlaufzeiten, Umlaufvermögen, Lagerstände und –drehungen untersucht um etwaige Verbesserungspotenziale zu erkennen. Ebenso wurde das Produktionssystem analysiert und eine Value Stream Analyse durchgeführt.
- Im zweiten Schritt wurde ausgehend von den Analyseergebnissen Schwerpunktthemen definiert die sich mit der Optimierung der Rüstzeiten bei einer Engpassmaschine und den Produktivitäten bei mehreren Fertigungslinien beschäftigen.
- Dafür wurden kritische Erfolgskennzahlen (KPI’s – Key Performance Indicators) festgelegt die über wöchentlich aktualisierte Monitoringsysteme überwacht werden konnten. Diese, von uns „Dashboards“ genannten Leistungsspiegel, wurden für alle, direkt am eigenen Arbeitsplatz, öffentlich zugänglich gemacht.
- Nachdem die Ziele klar definiert waren, wurde in jedem der spezifizierten Bereiche mit Verbesserungsprojekten begonnen.
Um die Produktivität massiv zu erhöhen, als Zielsetzung wurden +25% bis +35% festgelegt, musste der komplette Fertigungsablauf überarbeitet werden.
Zusammenfassend wurden folgende Aktivitäten durchgeführt:
- Einführung des Ziehsystems, d.h. die Produkte werden vom nachfolgenden Produktionsschritt angefordert.
- Einführung einer Taktung um Stillstände von Maschinen bzw. Wartezeiten von Personal zu vermeiden.
- Veränderung des Produktionslayouts um einen durchgängigen „Fluss“ zu erreichen.
- Reduktion von Verschwendung (Muda) bei jedem Arbeitsschritt.
- Einführung von KVP-/Kaizen Teams mit täglichen Verbesserungsmeetings vor Ort.
Ergebnisse:
Das Projekt wurde Anfang 2007 gestartet, der Großteil der notwendigen Adaptionen wurde bis Mitte 2007 durchgeführt und anschließend erfolgte bis Ende des 3. Quartals der Feinschliff in manchen Bereichen. Folgende Ergebnisse konnten realisiert werden:
Net Benefit: 315.000 € p.a.
Reduktion Losgrößen: um -50% bis -80%
Reduktion Durchlaufzeiten: um -80%
Erhöhung Produktivität (gemessen als Stück je Mannstunde): +32% bis +86%
Die Effekte auf den Lagerstand, die Qualität, die Verfügbarkeit und die Flexibilität können erst im nächsten Jahr gemessen werden und werden aus der Erfahrung nochmals einen wesentlichen Benefit bringen.